Top Core Lamination Stacks Manufacturer in China
As China’s premier manufacturer of lamination stacks, Sino understands that high-quality core lamination stacks are pivotal to unlocking peak efficiency and minimizing energy loss. Drawing on our decades of magnetic research and industry expertise, we’ll craft precision magnetic cores for you, engineered to genuinely elevate your product’s performance!
Sino: Lamination Stack Leaders in China
At Sino, we understand that the heart of any type of effective motor, transformer, or electromagnetic device beats stronger with precisely crafted core laminations. Our strength depends on a powerful mix of deep product proficiency– from picking the optimum grade of silicon steel, be it non-oriented or grain-oriented (GOES), to using remarkable insulation– and innovative production.
We’re discussing ultra-thin laminations, down to 0.1 mm for high-frequency scenarios, attained with precision marking or laser cutting, adhered to by stress-relieving annealing and careful setting up strategies like interlocking, bonding, or regulated welding.
Why choose Sino? Our track record speaks volumes. We have actually helped clients achieve substantial reductions in core losses– as an example, one industrial electric motor client saw a 4% decrease, leading to cooler operation and higher outcome. Our capacity to tailor lamination stacks to your precise specs, whether for basic E&I forms or complex, bespoke designs for EV grip motors or clinical gadgets, establishes us apart.
15+ years of manufacturing experience
12,000 square meters of modern plant
33 units of various large equipment
Sino's Precision Engineering
The number one reason for using lamination stacks is to slash those energy-sapping eddy current losses, and this is where Sino's attention to detail truly shines. The thinner the lamination, the more effectively we can suppress these currents, especially in high-frequency scenarios.
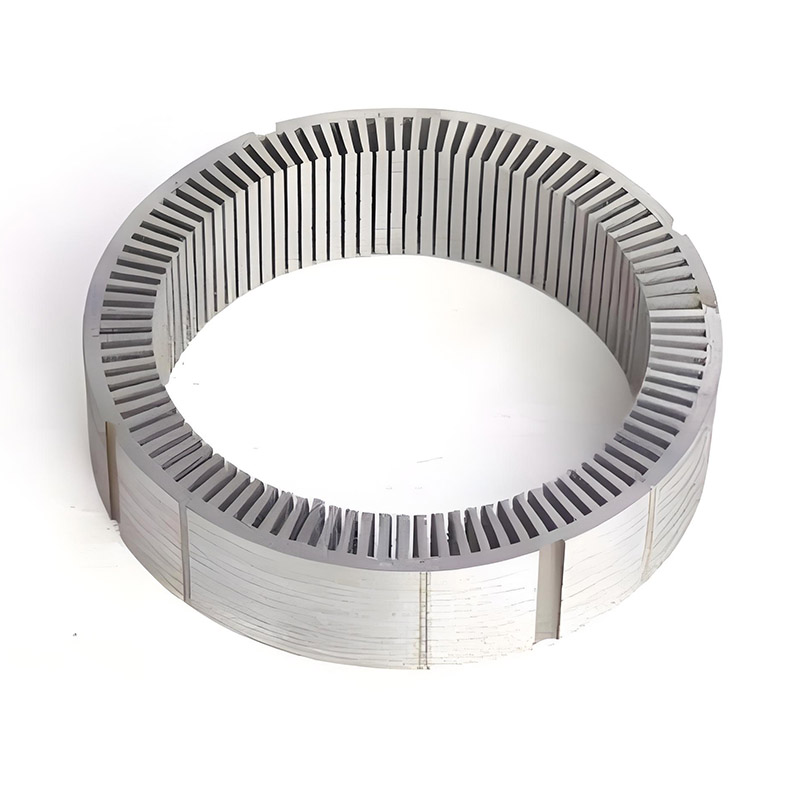
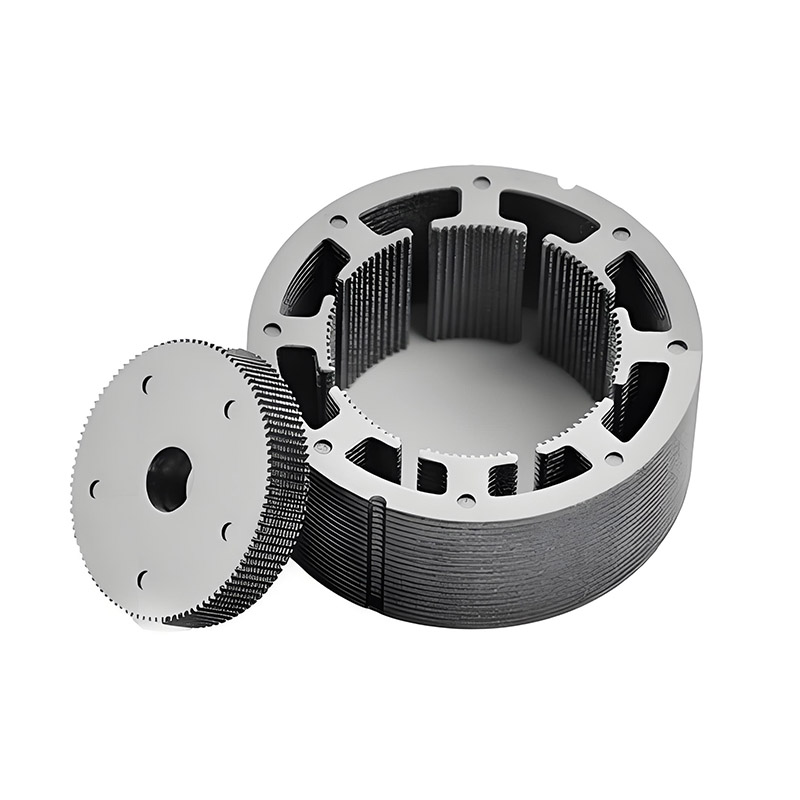
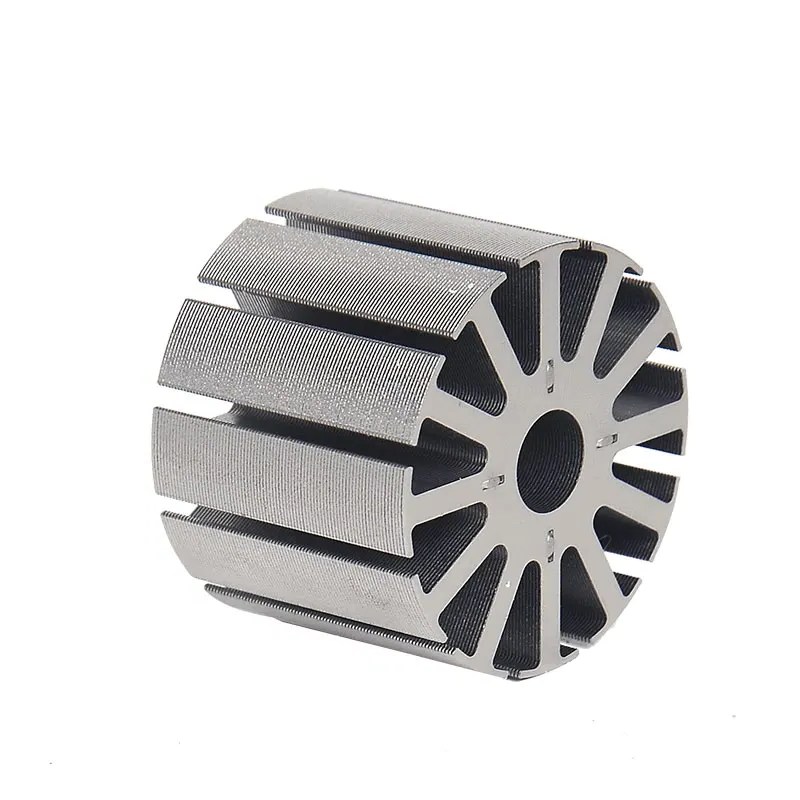
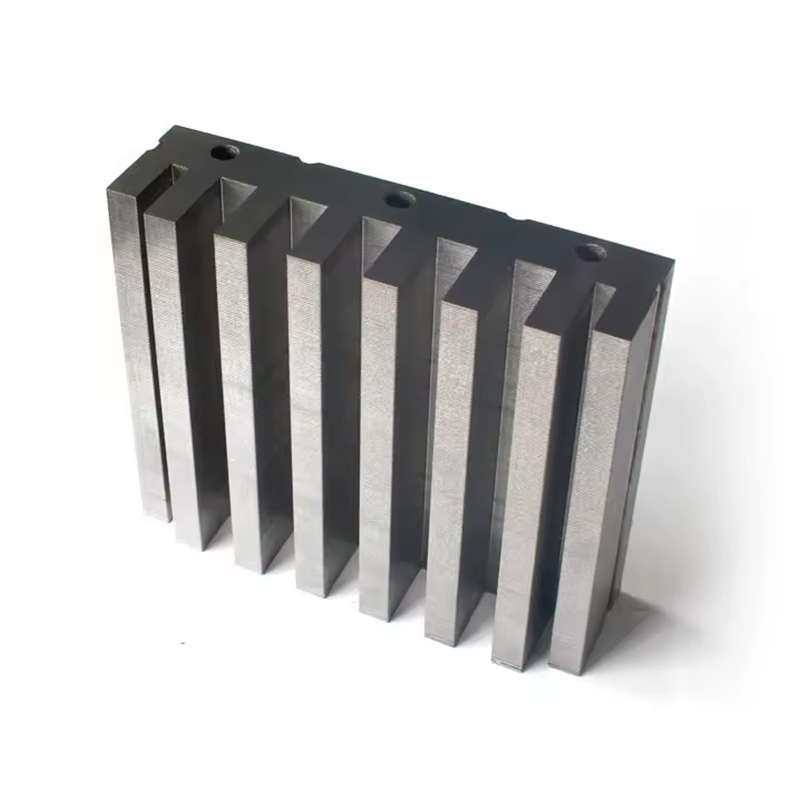
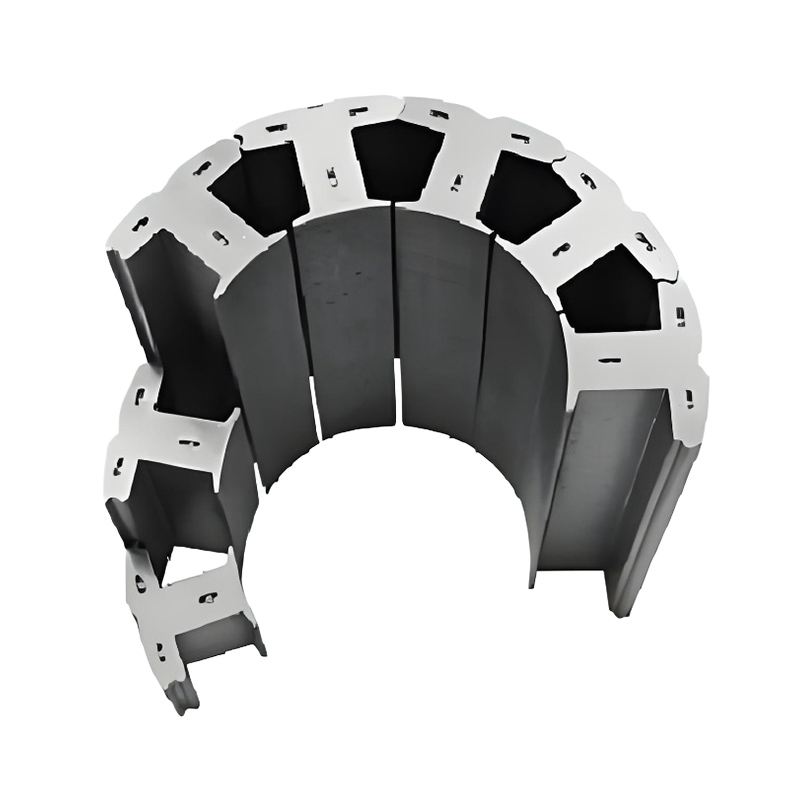
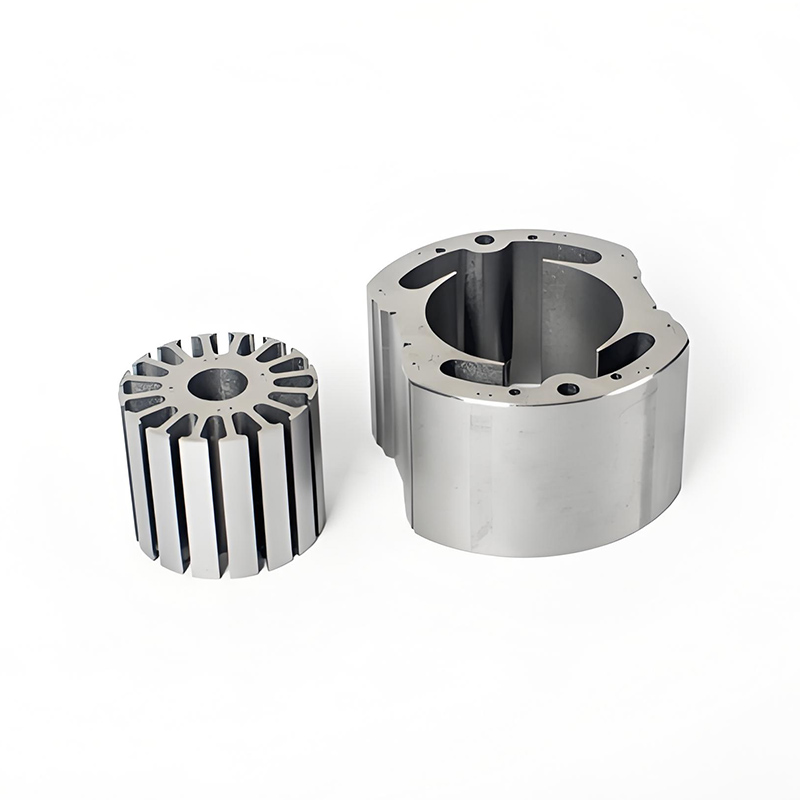
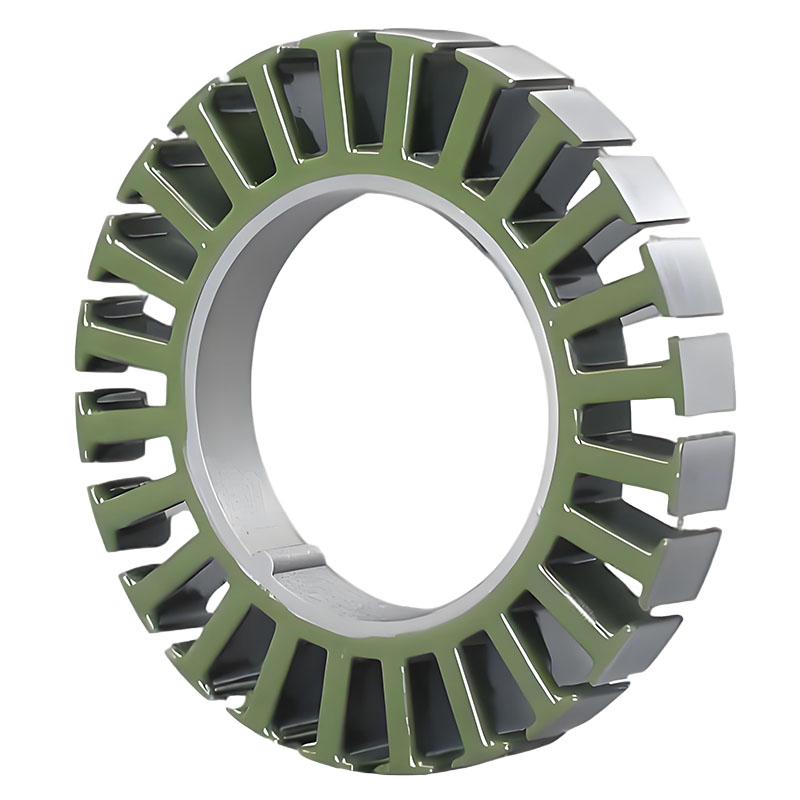

Sino's Material Portfolio
We understand that different scenarios demand different material grades.
Non-Oriented Electrical Steel
Perfect for devices where the magnetic field is constantly changing direction, like in the rotating parts of motors and generators. Sino ensures consistent quality for these dynamic applications.
Grain-Oriented Electrical Steel (GOES)
This stuff is special. It has superior magnetic properties along a specific grain direction achieved during its rolling process. This makes it the champion for transformer core laminations, where the magnetic flux generally follows a well-defined path. Sino can supply precisely cut GOES laminations that maximize transformer efficiency.
Data-Driven Decisions (Simplified Material Impact)
Material Property | Effect of Silicon (Si) in Steel | Sino’s Focus for Your Benefit |
Electrical Resistivity | Increases Significantly | Maximizes eddy current reduction |
Magnetic Permeability | Remains High | Ensures easy, efficient magnetization |
Coercivity | Decreases | Minimizes hysteresis energy loss |
Saturation Flux Density | Slight Decrease | Managed for optimal performance |
When you talk to Sino, we don’t just sell you steel; we discuss your application to help you select the optimal grade for your lamination stacks, ensuring you get the best performance-to-cost ratio.
How Sino Builds Superior Laminated Cores
Having the right material is one thing; shaping it and assembling it with precision is another. Sino’s manufacturing floor is a hub of advanced technology and skilled craftsmanship.
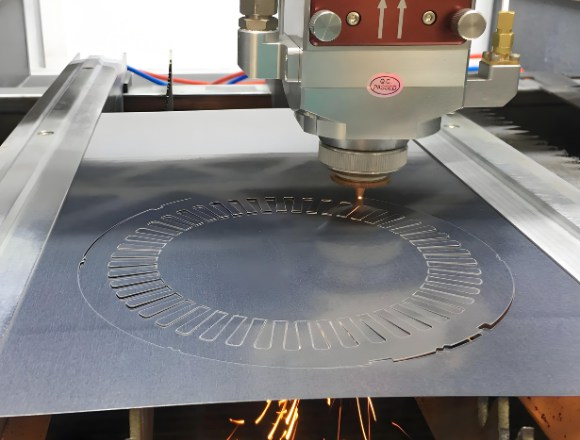
Precision Cutting
Whether it’s high-speed stamping for large volume orders of standard E&I core laminations, or intricate laser cutting for custom prototypes or complex motor stator/rotor shapes, Sino has the technology. We meticulously maintain our stamping dies to minimize burrs – those tiny metal whiskers that can pierce insulation and create shorts. For a recent project involving a uniquely shaped magnetic lamination for a medical imaging device, our laser cutting capabilities allowed the client to iterate through designs rapidly without incurring massive tooling costs.

Stress Relief (Annealing)
The process of stamping or cutting can introduce mechanical stresses into the steel, which can mess with its magnetic properties. Sino incorporates controlled annealing (heat treatment) processes to relieve these stresses, restoring the material to its optimal magnetic state. This ensures your laminated core performs as expected, not just looks the part.
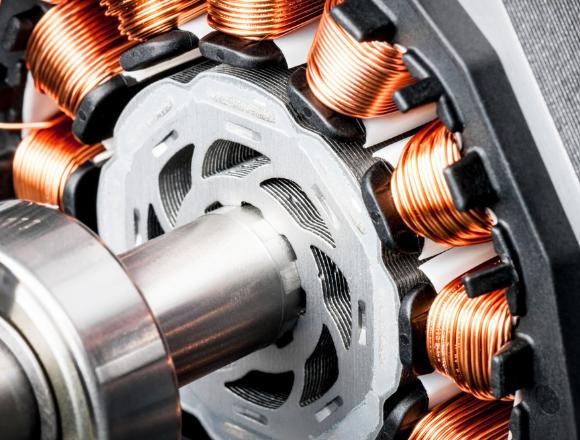
Stacking & Joining with Integrity
How the individual lamination stacks are held together is crucial.
- Interlocking: A cost-effective mechanical method where small protrusions on one lamination lock into corresponding indentations on the next. Sino’s tooling ensures these interlocks are precise and secure.
- Bonding: Using specialized adhesives to glue the stack together. This can offer excellent insulation integrity, add mechanical rigidity, and even help with noise reduction. Sino has experience with various bonding agents suitable for different operating temperatures and stresses.
- Welding: While it needs to be done carefully to avoid creating localized shorts between laminations (which would defeat the purpose!), welding is often used for robustness, especially along the outer edges of a stack. Sino’s welding processes are tightly controlled to minimize any negative impact on inter-laminar resistance.
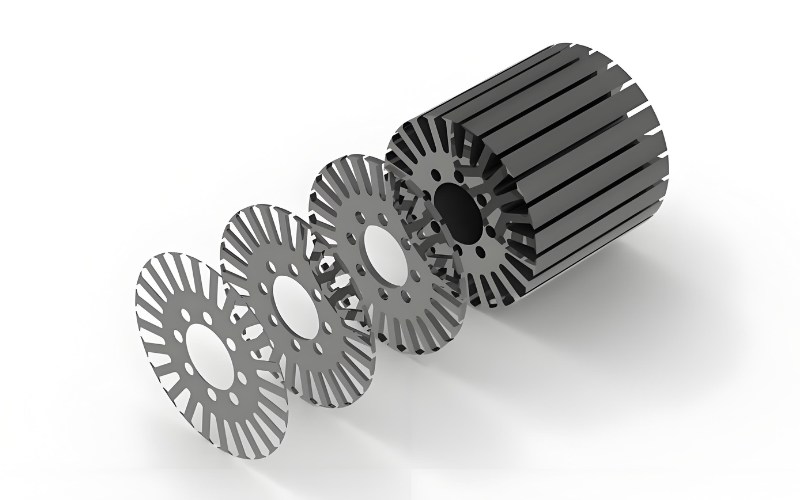
Maximizing the Stacking Factor
No stack is 100% dense metal due to the insulation layers and tiny air gaps. The “stacking factor” (typically 93-97%) tells you how much actual magnetic material you have. Sino strives to maximize this through precise coating thickness control and careful assembly, meaning you get more magnetic punch for a given stack volume.
Lamination Core Manufacturer - Sino's Capability
We’re not a one-size-fits-all shop. For standard 50/60 Hz applications – think the motors in your workshop tools or neighborhood transformers – we typically produce core laminations with thicknesses from 0.35mm to 0.65mm.
But the modern world is demanding more. For instance, a client developing a cutting-edge, high-frequency switched-mode power supply for server farms approached us. Their design required minimal losses at much higher operating frequencies.
Sino rose to the challenge, engineering ultra-thin magnetic laminations down to 0.1mm, complete with a specialized high-resistivity insulation. The result? Their prototype exceeded efficiency targets, running cooler and more reliably than they’d hoped.
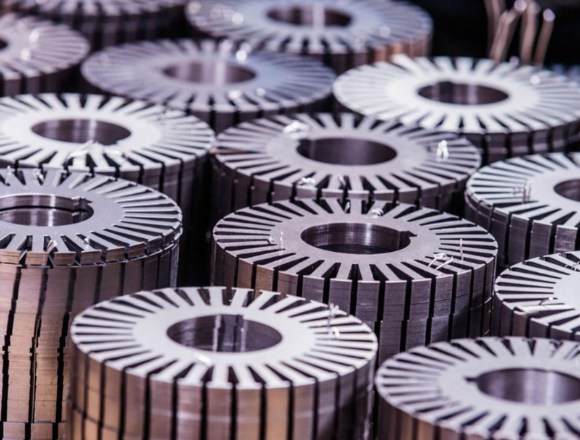
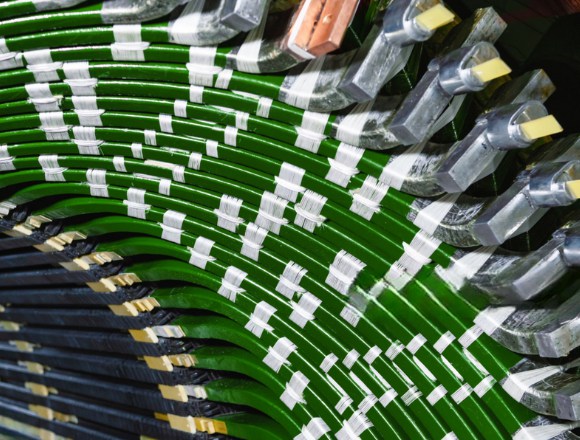
Laminated Core Insulation Integrity
That tiny layer of insulation is everything. Sino employs advanced coating techniques and rigorous quality checks to ensure there are no breaches or inconsistencies that could compromise the electrical separation between laminations.
Sino's Expertise in Electrical Steels
The metal itself is a critical piece of the puzzle. You can’t just use any old steel. Sino sources and works with specialized silicon steel (often called electrical steel) because its properties are tailor-made for lamination stacks.
Adding a small percentage of silicon (usually 1-4%) to iron works wonders: it significantly increases the steel’s electrical resistivity, further hindering those pesky eddy currents. It also helps to reduce another gremlin called hysteresis loss – the energy it takes to magnetize and demagnetize the core material with each AC cycle.
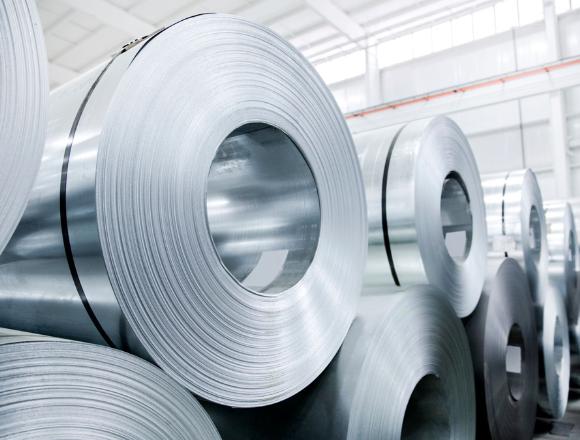
Sino's Customization for Your Unique Needs
The world of electromagnetics is diverse, and so are the requirements for lamination stacks. Sino isn’t just about standard parts; we thrive on customization.
Shapes and Sizes Galore
From common E, I, and UI shapes for transformers and inductors, to intricate toroidal (donut-shaped) laminated cores for high-performance power supplies, to fully custom-designed rotor and stator core laminations for specialized motors – if you can design it, Sino can likely figure out how to make it efficiently.
Specialized Coatings
Beyond standard electrical insulation, perhaps your scenario involves a harsh environment requiring enhanced corrosion resistance, or a specific dielectric strength. Talk to us! Sino can explore specialized coating options.
End-to-End Support
We see ourselves as more than just a supplier; we're your partner in core technology. From initial design consultation, material selection advice, prototyping, to full-scale production and quality assurance, Sino is with you every step of the way. You bring the electromagnetic challenge; Sino provides the optimized lamination stacks to solve it.
Where Sino's Lamination Stacks Power Progress
The applications for high-quality lamination stacks are virtually endless. Here are just a few scenarios where Sino's products make a critical difference:
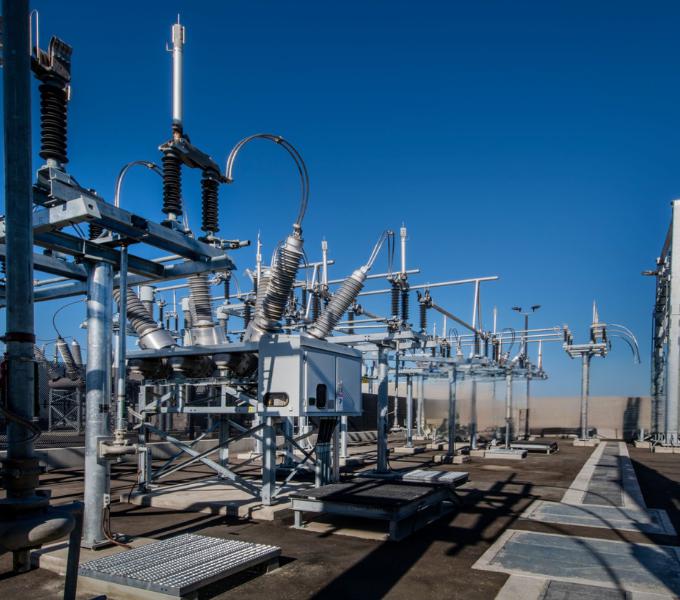
Transformers
From massive power distribution transformers handling megawatts to the small ones in your phone charger, laminated cores (especially those from Sino using prime GOES) are essential for efficient voltage conversion with minimal energy loss.
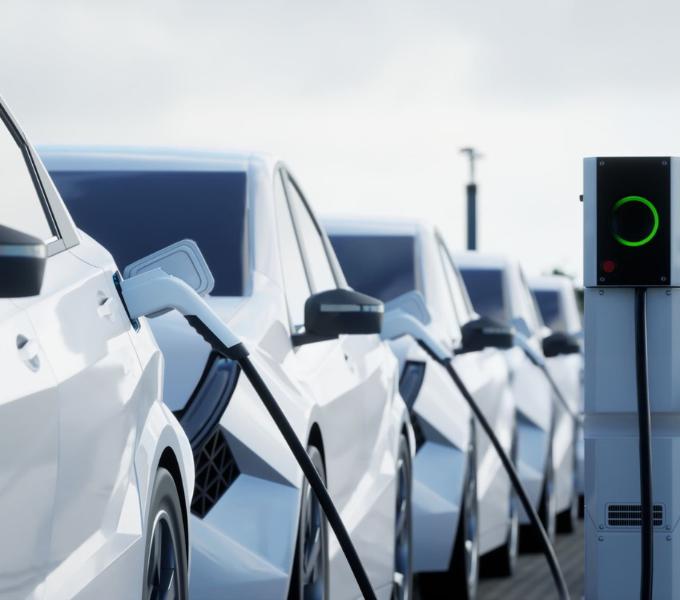
Electric Motors
Every induction motor, brushless DC motor, or synchronous motor relies on precisely stacked core laminations for its stator and rotor. One automotive Tier 1 supplier worked with Sino to develop a new traction motor laminated core design that improved torque density by 7% through optimized slot geometry and material selection.
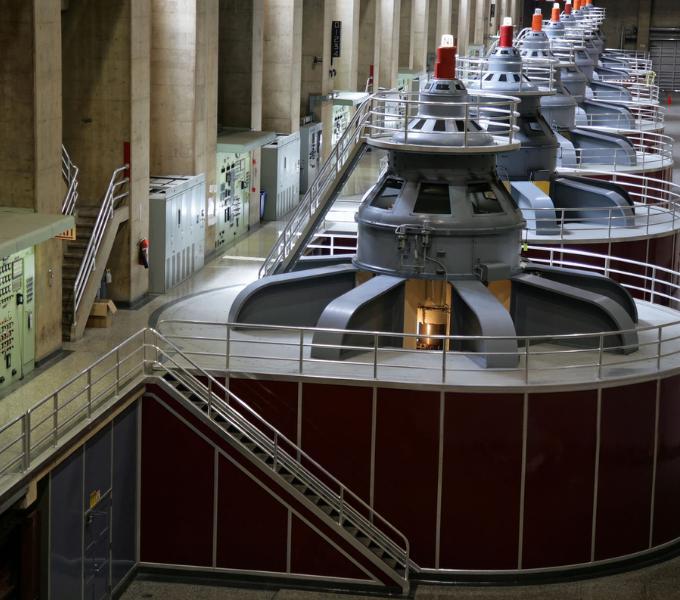
Generators
Whether it's a colossal generator in a hydroelectric dam or a wind turbine spinning atop a hill, efficient lamination stacks are key to converting mechanical energy into electrical energy with minimal losses.
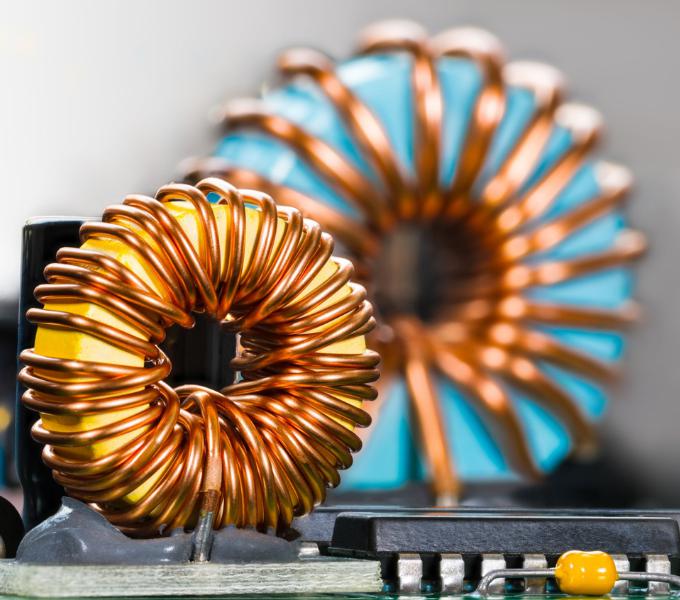
Inductors and Chokes
In power electronics, these components are vital for conditioning power, and their performance hinges on the quality of their magnetic lamination based cores. Sino provides cores that ensure stable inductance and low losses in these demanding circuits.
Ready to Power Up Your Next Project?
Sino’s lamination stacks are designed to help your products perform better, last longer, and operate more efficiently. If you’re designing or manufacturing any device that relies on electromagnetic principles, the quality of your laminated core is non-negotiable. Don’t let inefficient cores rob your products of their potential.
Let's Discuss Your Laminated Core Project!
Contact Sino today. Let’s discuss your specific scenario and explore how our expertly crafted lamination stacks can provide the efficient, reliable heart your application deserves. We’re excited to help you build the next generation of electrical and electronic marvels!
- [email protected]
- +86 17727849205
- Xinggang Tongchuanghui, No. 6099 Baoan Avenue, Xinhe Community, Fuhai Street, Baoan District, Shenzhen
Note: To speed up your project, you can label Lamination Stacks with details such as tolerance, material, surface finish, whether or not oxidized insulation is required, quantity, and more.
Certificates Obtained by Sino
Each certificate represents the results and strengths we have gained in the field of lamination stacks!
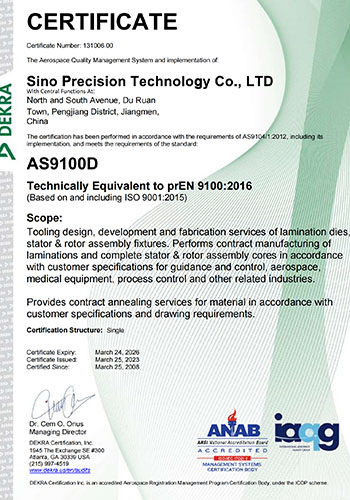
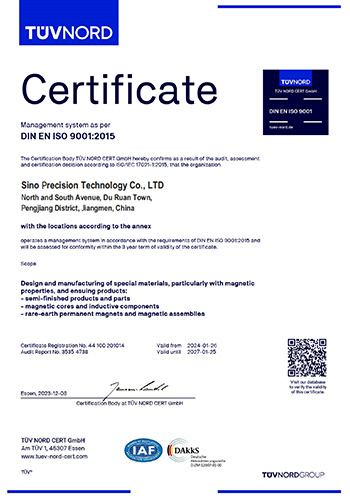
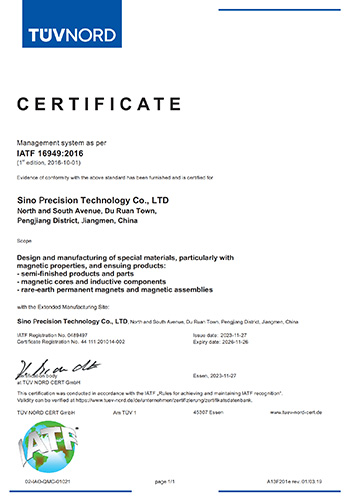


What Our Client’s Say
" We work with a massive range of transformer tasks, so we need a distributor who can deal with diverse product demands and customized layouts, usually on limited timetables. Sino has actually shown to be unbelievably adaptable and dependable for us. They consistently deliver high-grade lamination stacks, whether it's a conventional order or something very specialized. It makes my job a great deal much easier knowing I can rely on them."
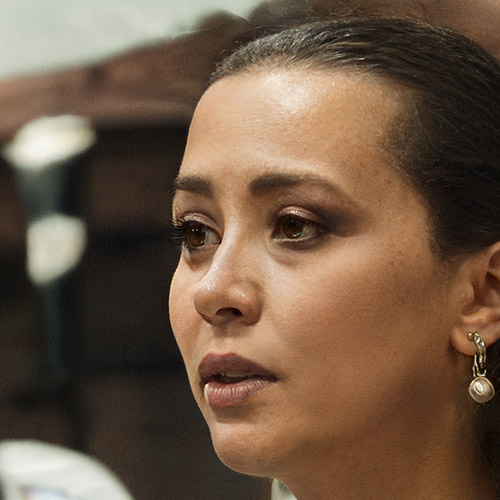
" In our area, there's absolutely no space for concession on quality or uniformity. We build delicate medical imaging equipment, and the elements have to be remarkable. Sino's lamination heaps have fulfilled our extremely rigorous quality control requirements for every little thing from our specialized transformers to little motor settings up. We appreciate their attention to information; it provides us peace of mind."
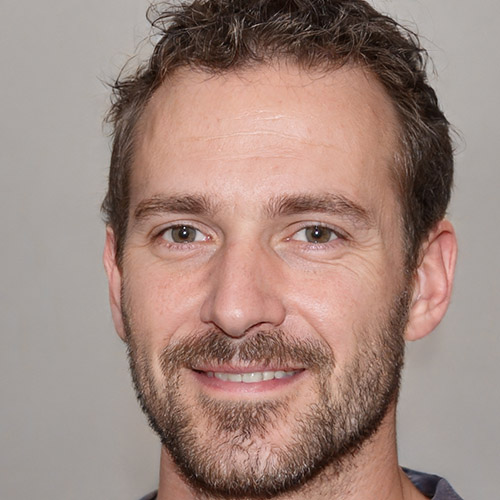
" When we're developing our next generation of EV electric motors, efficiency is absolutely everything. Sino's lamination heaps have actually consistently offered us the accuracy and worldly top quality we require to press effectiveness limits. Truthfully, their consistency and on-time shipment simply make our lives a whole lot easier. It's a true collaboration."
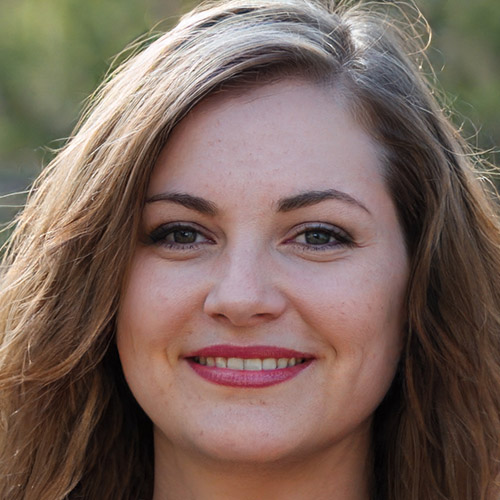
" Running our robotics production line smoothly implies we need elements that are entirely reputable. Sino's lamination heaps are specifically that. We usually have extremely certain needs for our personalized robotic joints, and they've always supplied easily. It's terrific to have a supplier where you recognize the top quality will certainly exist, each time."
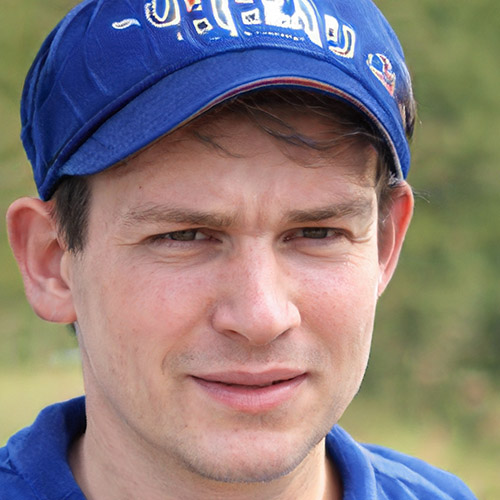
" For our massive solar inverter projects, efficiency and long life are crucial, but so is handling costs. Sino has been a fantastic partner on both fronts. Their laminations help us develop really reputable systems, and their prices incorporated with constant distribution assists us hit our project spending plans and timelines. They make the supply chain facet much less difficult."
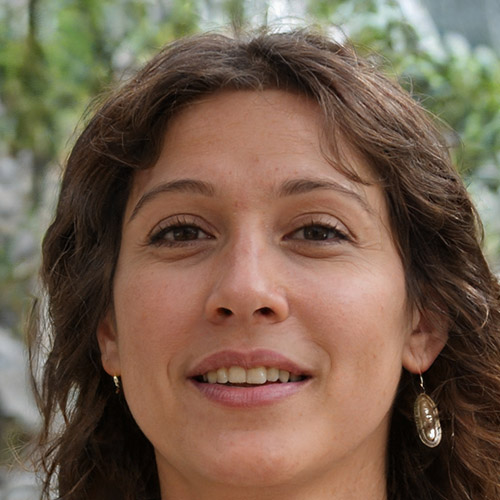
Frequently Asked Questions
At Sino, top quality is our top concern. We apply an extensive three-stage quality control process:.
- Inbound Product Examination: We test raw electrical steel for metallurgical composition, density, and magnetic residential properties upon arrival.
- In-Process Tracking: Our assembly line are outfitted with real-time monitoring and accuracy tooling, with routine dimensional and visual inspections by trained professionals.
- End Product Testing: Every set undergoes extensive testing, including precise dimensional checks, burr elevation measurements, interlamination resistance tests, and core loss measurements (where suitable) to guarantee it satisfies or surpasses specified demands. We are ISO 9001 accredited, guaranteeing our procedures are constantly managed and enhanced.
Absolutely. Personalization is just one of our core strengths. Our knowledgeable engineering team functions very closely with customers using sophisticated CAD/CAM software to convert complex styles into precise manufacturing procedures. We have comprehensive experience working with a vast array of electric steel grades, including different M-series steels (e.g., M19, M27, M36), non-grain oriented (NGO) steels, and high-permeability alloys, suiting different densities and surface area coatings to satisfy particular magnetic efficiency and application requirements.
Normal lead times can differ depending on the intricacy of the layout, product availability, and order volume. For basic products, it’s typically 4-6 weeks from order verification. For custom-made layouts or high-volume tasks, we’ll give a comprehensive manufacturing schedule. We make sure on-time distribution through efficient manufacturing planning, calculated resources inventory management, and solid partnerships with trustworthy logistics providers. We additionally maintain transparent communication with our customers, providing normal updates on order condition.
Our affordable rates is a result of numerous aspects, not a compromise on quality. We accomplish cost-effectiveness through:.
- Lean Production Concepts: Enhancing our manufacturing processes to reduce waste and take full advantage of effectiveness.
- Volume Investing In: Leveraging our range to safeguard resources at better costs.
- Advanced Automation: Using modern-day equipment that improves accuracy and lowers labor prices.
- Skilled Workforce: Our seasoned team makes certain very little mistakes and revamp. We focus on providing phenomenal value — high-quality lamination heaps that carry out accurately, helping our consumers reduce their overall item expenses and enhance efficiency.
Shielding our customers’ intellectual property is paramount to building trust fund and long-term partnerships. We have strict internal procedures in place:.
- Non-Disclosure Agreements (NDAs): We are always prepared to sign formal NDAs prior to any kind of design info is shared.
- Secure Data Management: All customer layouts and requirements are kept on secure, access-controlled servers.
- Restricted Accessibility: Only accredited personnel straight involved in your job have access to your certain style documents.
- Worker Training: Our team is on a regular basis educated on privacy and IP protection plans. We understand the worth of your developments and are committed to guarding your proprietary details.
Discover Insights on Sino Laminated Cores Blogs
Step into our world of high-performance electrical steel laminations. The Sino Blog is dedicated to sharing our profound expertise and the latest developments in precision manufacturing of lamination stacks. Expect to find articles on crucial topics such as optimizing core efficiency, understanding diverse material properties.
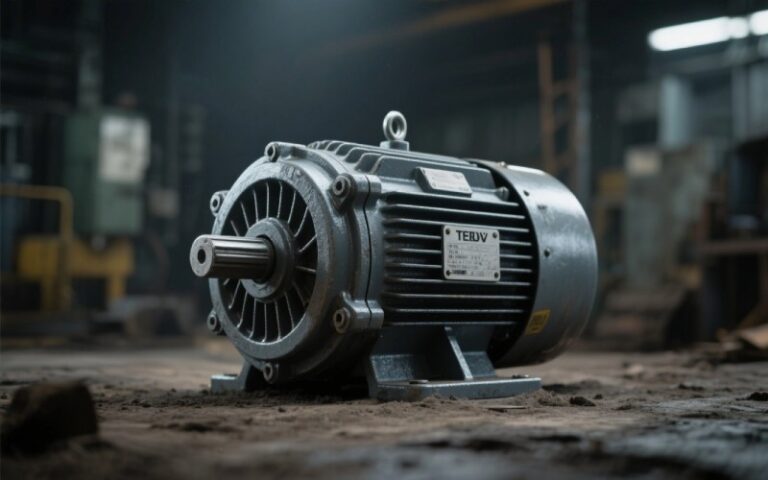
What is a TENV Motor? A Simple Definition of a Totally Enclosed Non-Ventilated Motor
Over the years, I have worked with many different machines. I have learned that an electric motor is the…
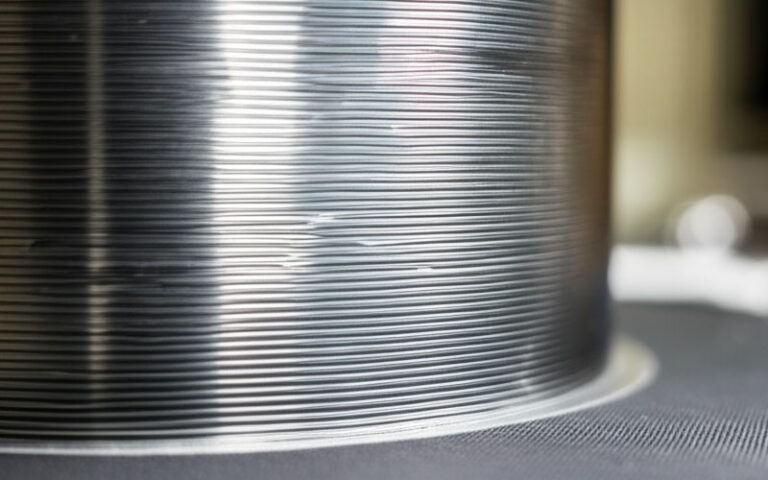
Adhesive Silicon Steel: My Journey Into Efficient Motor and Transformer Technology
Discovering Adhesive Silicon Steel When I first started working as an electrical engineer, I was amazed by how small…
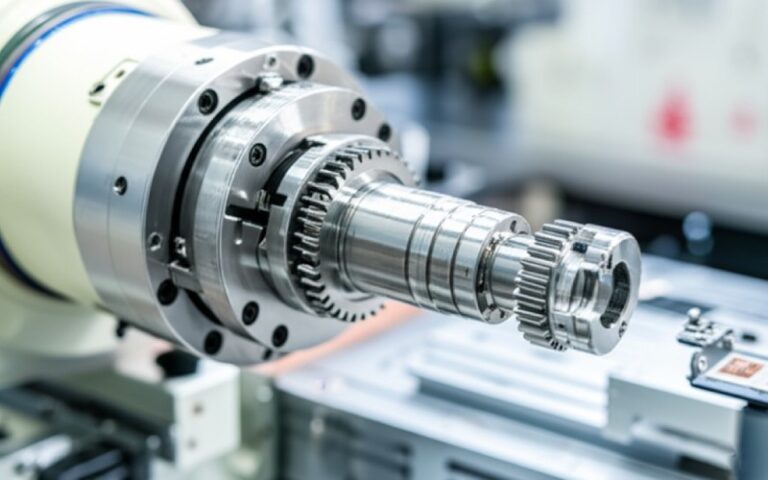
How Does a Servo Motor Work? A Simple Guide for Robots and Factory Work
A servo motor makes things move with very exact movement. How does a robot arm know the right place…